プロフィール
工藤
その他
プロフィール詳細
カレンダー
検索
アーカイブ
アクセスカウンター
- 今日のアクセス:673
- 昨日のアクセス:710
- 総アクセス数:4662769
▼ ルアー開発日記 タピオスF (その1)
- ジャンル:釣り具インプレ
先日HALへ行き打ち合わせの結果、タピオスのフローティングを作ることになりました。
数年前に、ハルシオンシステム(現HAL)から「港湾で使える7cmのスタンダードミノー」を作ってほしいと言われ、初めて樹脂ブランクルアーの開発&プロデュースをさせて戴きました。
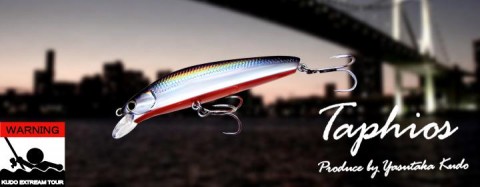
http://www.halcyon.jp/products/products_01.php?pro_id=132&ca_1_id=5&e=
当時は樹脂ルアーの開発が、どのような段階を踏んでいくかを全く知らなかったので、なかなか思うように進まなかったり・・・と、大変な思いでの開発となりました。
ただ、本業がプラスチック射出成型&金型を作製しているという事もあり、自分なりの「詰めていく仕事」は出来たんじゃないかと思います。
これから始まる、タピオスフローティングの話をする前に、ざっくりと樹脂ルアー作りのプロセスの紹介をしておきます。
なお、「一般的に」と言う括りですが、ハンドメイドルアーの作り方が多くあるように、樹脂ルアーの作り方も色々とあります。
また、「仕事の仕方は一つではない」のは、当たり前のこととして、とらえてください。
その中で、私がどうやって開発業務を進めていくか・・・の話を、これから数回に分けて紹介していくものです。
1 企画
マーケットが先か、他からの要望が先かはそれぞれですが、「作りたいルアー」を決めます。
並行して「どうやって売るか」を決めます。
まぁ、夢を語る部分ですねw
2 設計及び開発
樹脂製の製品は、金型を用いた射出成型で作られます。
イメージとしては、熱で溶けて液状化したABS(等)を金型へ押し込み(射出)、金型に熱が奪われ(冷却)て固形化したものを取り出します。(工程、数十秒。これを1Shotサイクルという)
大事なのは、金型の寸法と成型条件(量・圧力・時間)です。
特に金型は成型品の命で、高額なうえに一度作ってしまうと大幅な変更はできません。
その金型を作るうえで「製品設計図面の作成」は非常に重要なプロセスとなります。
では、その製品図面はどうやって作られるのかですが、これは実は様々なアプローチ方法があります。
昔から行われている一般的な方法では、モックというサンプルをまず作ります。
それは木が多く用いられます。
簡単に言えば、ウッドのハンドメイドを先に作るのです。
形状、アクションを含めて、欲しいものを一本作ってしまうのです。
それを精密測定して、製品図面(CAD)を起こし、金型を作ります。
タピオスはこのやり方でした。
モックサンプルは自分で作りました。
ちなみに図面は、現在はほぼすべてのメーカーが3Dデータで起こします。
そういうソフトがあり、その形状で予測される「収縮率や変形」を考慮して、金型を作ります。
成形屋の視点で言わせていただけると、ルアー形状とは結構難しい製品です。
リブの収縮による変形(厚みのある部分は冷えにくく熱を持つので、収縮が遅れることになり、その為にヒケや引っ張られる力が発生する)が発生しやすく、製品図面から金型図面への転換にはそれなりに気を使う必要がります。
製品形状がそのまま機能性に影響を及ぼすという部分も、難しさに輪をかけますね。
金型というものは、読んで字のごとく「金属の型」です。
ですから、一度削ってしまうと、元に戻すことはできません。
その為に、金型を作るときは「削り方向」の余裕度をもって、設計を行います。
金型は製品の真逆の形状なので、削り方向とは「製品を大きくする方向」の事を言います。
金型修正は、製品を小さくする加工はできないのです。
これは今では誰もが知っていることですが、ウッドと樹脂ブランクでは、同じ形状では同じアクションは出ません。
比重と重量配分が異なるからです。(細かい説明は省く)
ですから、モックの作成時からある程度の「作りたいルアーのためのサンプル」という事を念頭に行き、アクションや形状を決めていきます。
そういった部分は経験がものを言います。
最近は、このウッドによるモックサンプルを省き、樹脂の削り出しでサンプルを作るのが主流になりつつあります。
メリットは、金型を作る前に製品と同じ比重の樹脂(ABS等)でサンプルチェックを行う事で、より製品版に近い試作品を作ることができるという事です。
ただ、それなりにサンプル作るんはお高いですが。
また、まれに「試作サンプルなしでいきなり金型作成」というメーカーもあります。
類似品がすでにあって、そのコピー品を作るときや、とにかくコストをかけたくな場合です。
まぁ、悲しいけど、そういうメーカーも実際あるよという事で。
余談ですが、この設計開発のプロセスは、それぞれにアウトソーシングすることがあります。(というか、みんなします)
メーカーは企画・販売のみで、物を創るにあたっての工程は「すべてを外注で行う」というのも、珍しい話ではありません。
これは良い悪いではなく、例えばCADを用いた設計なんてものを、1から教えて(勉強して)いたらかなりの時間がかかってしまいます。
ですから、業界の中に「その専門のプロ」が存在します。
どこまで投げるか(設計のみか、モックから全てか)は、メーカーの考え方です。
タピオスを作った当時は、設計のみ投げていましたが、今は社内に超優秀な設計がいます。(今回の話しの本筋とは異なるので詳しくは言いませんが、決まったものを図面に起こすだけの設計と、ルアーというものを理解している人が起こす設計は、天と地ほどの差が出ます。)
3 金型発注・量産ブランク作成
金型や樹脂ブランクを自ら作っているメーカーは、それほど多くはありません。
多くのメーカーがアウトソーシングしています。
(ちなみに設計もアウトソーシングするメーカがほとんどです)
製品図面を金型屋さんへ渡し、金型を作ってもらいます。
ざっくりいうと、100万円ぐらい。
出来上がった金型を成形屋さんへ渡し、射出成型機で試作を行います。
成形の仕事は、金型取り付け→条件設定→成形→検査 です。
一個の製品を作るのにかかる時間は数十秒(1Shotサイクル)ですが、金型セットや設定にはある程度時間がかかります。
これを段取り時間と言い、段取り費がかかります。
その段取り費用は、製品一個あたりに乗っていきます。
ですから、「一回のLotで作る個数(MOQ)」が多いほど、成形費用は下がります。
MOQが小さいメーカー(あんまり売ってないメーカー)は、そこでちょっと辛いのです。
さて、試作サンプルブランク(樹脂製)が上がりましたので、今度は量産製品の試作です。
4 量産品試作
量産品とは、連続して同じものをたくさん作るから、量産と言います。
要は、「再現性がどれほどあるか」です。
樹脂ルアーのメリットは、この量産性にあります。
前出しましたが、金型と成型条件が一緒ならば、射出成型とは同じ製品が速く安く作ることができるからです。
ただ、成形条件が変われば、当然ですが「金型が同じでも異なるものができる」可能性もあります。
劇的に変わるのが「製品重量」です。
「昔のとアクションが違う」なんてルアーがたまにありますが、金型の変更がない場合は成型条件や部材の変更があります。
試作のやり方ですが、まずはファーストトライ(新規金型で最初に作った樹脂ブランク)で出来上がってきたブランクをチェックします。
主にヒケやウェルド(樹脂結合が最後に行われる部分)や最終充填位置をチェクします。
強度的に不安があったりした場合は、ここでもう一回の成形トライをしてもらいます。
大事なのは、とにかく見落とさない事。
この後の部材を組んでのアクションチェックで「これで決まり」となってしまうと、もう成型条件は変更ができません。
問題がない場合は、組み付けトライへ移ります。
量産で使う「ウェイト」「ワイヤー」を組み込み、塗装工程を実際に行います。
組み付け上の不具合はないか?
部材の不具合はないか?
等です。
問題がなければ、次のフィールドテストとなります。
つづく
数年前に、ハルシオンシステム(現HAL)から「港湾で使える7cmのスタンダードミノー」を作ってほしいと言われ、初めて樹脂ブランクルアーの開発&プロデュースをさせて戴きました。
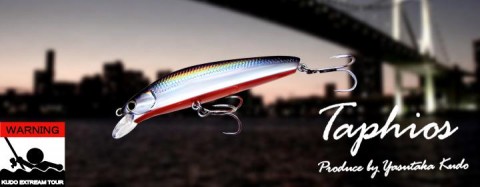
http://www.halcyon.jp/products/products_01.php?pro_id=132&ca_1_id=5&e=
当時は樹脂ルアーの開発が、どのような段階を踏んでいくかを全く知らなかったので、なかなか思うように進まなかったり・・・と、大変な思いでの開発となりました。
ただ、本業がプラスチック射出成型&金型を作製しているという事もあり、自分なりの「詰めていく仕事」は出来たんじゃないかと思います。
これから始まる、タピオスフローティングの話をする前に、ざっくりと樹脂ルアー作りのプロセスの紹介をしておきます。
なお、「一般的に」と言う括りですが、ハンドメイドルアーの作り方が多くあるように、樹脂ルアーの作り方も色々とあります。
また、「仕事の仕方は一つではない」のは、当たり前のこととして、とらえてください。
その中で、私がどうやって開発業務を進めていくか・・・の話を、これから数回に分けて紹介していくものです。
1 企画
マーケットが先か、他からの要望が先かはそれぞれですが、「作りたいルアー」を決めます。
並行して「どうやって売るか」を決めます。
まぁ、夢を語る部分ですねw
2 設計及び開発
樹脂製の製品は、金型を用いた射出成型で作られます。
イメージとしては、熱で溶けて液状化したABS(等)を金型へ押し込み(射出)、金型に熱が奪われ(冷却)て固形化したものを取り出します。(工程、数十秒。これを1Shotサイクルという)
大事なのは、金型の寸法と成型条件(量・圧力・時間)です。
特に金型は成型品の命で、高額なうえに一度作ってしまうと大幅な変更はできません。
その金型を作るうえで「製品設計図面の作成」は非常に重要なプロセスとなります。
では、その製品図面はどうやって作られるのかですが、これは実は様々なアプローチ方法があります。
昔から行われている一般的な方法では、モックというサンプルをまず作ります。
それは木が多く用いられます。
簡単に言えば、ウッドのハンドメイドを先に作るのです。
形状、アクションを含めて、欲しいものを一本作ってしまうのです。
それを精密測定して、製品図面(CAD)を起こし、金型を作ります。
タピオスはこのやり方でした。
モックサンプルは自分で作りました。
ちなみに図面は、現在はほぼすべてのメーカーが3Dデータで起こします。
そういうソフトがあり、その形状で予測される「収縮率や変形」を考慮して、金型を作ります。
成形屋の視点で言わせていただけると、ルアー形状とは結構難しい製品です。
リブの収縮による変形(厚みのある部分は冷えにくく熱を持つので、収縮が遅れることになり、その為にヒケや引っ張られる力が発生する)が発生しやすく、製品図面から金型図面への転換にはそれなりに気を使う必要がります。
製品形状がそのまま機能性に影響を及ぼすという部分も、難しさに輪をかけますね。
金型というものは、読んで字のごとく「金属の型」です。
ですから、一度削ってしまうと、元に戻すことはできません。
その為に、金型を作るときは「削り方向」の余裕度をもって、設計を行います。
金型は製品の真逆の形状なので、削り方向とは「製品を大きくする方向」の事を言います。
金型修正は、製品を小さくする加工はできないのです。
これは今では誰もが知っていることですが、ウッドと樹脂ブランクでは、同じ形状では同じアクションは出ません。
比重と重量配分が異なるからです。(細かい説明は省く)
ですから、モックの作成時からある程度の「作りたいルアーのためのサンプル」という事を念頭に行き、アクションや形状を決めていきます。
そういった部分は経験がものを言います。
最近は、このウッドによるモックサンプルを省き、樹脂の削り出しでサンプルを作るのが主流になりつつあります。
メリットは、金型を作る前に製品と同じ比重の樹脂(ABS等)でサンプルチェックを行う事で、より製品版に近い試作品を作ることができるという事です。
ただ、それなりにサンプル作るんはお高いですが。
また、まれに「試作サンプルなしでいきなり金型作成」というメーカーもあります。
類似品がすでにあって、そのコピー品を作るときや、とにかくコストをかけたくな場合です。
まぁ、悲しいけど、そういうメーカーも実際あるよという事で。
余談ですが、この設計開発のプロセスは、それぞれにアウトソーシングすることがあります。(というか、みんなします)
メーカーは企画・販売のみで、物を創るにあたっての工程は「すべてを外注で行う」というのも、珍しい話ではありません。
これは良い悪いではなく、例えばCADを用いた設計なんてものを、1から教えて(勉強して)いたらかなりの時間がかかってしまいます。
ですから、業界の中に「その専門のプロ」が存在します。
どこまで投げるか(設計のみか、モックから全てか)は、メーカーの考え方です。
タピオスを作った当時は、設計のみ投げていましたが、今は社内に超優秀な設計がいます。(今回の話しの本筋とは異なるので詳しくは言いませんが、決まったものを図面に起こすだけの設計と、ルアーというものを理解している人が起こす設計は、天と地ほどの差が出ます。)
3 金型発注・量産ブランク作成
金型や樹脂ブランクを自ら作っているメーカーは、それほど多くはありません。
多くのメーカーがアウトソーシングしています。
(ちなみに設計もアウトソーシングするメーカがほとんどです)
製品図面を金型屋さんへ渡し、金型を作ってもらいます。
ざっくりいうと、100万円ぐらい。
出来上がった金型を成形屋さんへ渡し、射出成型機で試作を行います。
成形の仕事は、金型取り付け→条件設定→成形→検査 です。
一個の製品を作るのにかかる時間は数十秒(1Shotサイクル)ですが、金型セットや設定にはある程度時間がかかります。
これを段取り時間と言い、段取り費がかかります。
その段取り費用は、製品一個あたりに乗っていきます。
ですから、「一回のLotで作る個数(MOQ)」が多いほど、成形費用は下がります。
MOQが小さいメーカー(あんまり売ってないメーカー)は、そこでちょっと辛いのです。
さて、試作サンプルブランク(樹脂製)が上がりましたので、今度は量産製品の試作です。
4 量産品試作
量産品とは、連続して同じものをたくさん作るから、量産と言います。
要は、「再現性がどれほどあるか」です。
樹脂ルアーのメリットは、この量産性にあります。
前出しましたが、金型と成型条件が一緒ならば、射出成型とは同じ製品が速く安く作ることができるからです。
ただ、成形条件が変われば、当然ですが「金型が同じでも異なるものができる」可能性もあります。
劇的に変わるのが「製品重量」です。
「昔のとアクションが違う」なんてルアーがたまにありますが、金型の変更がない場合は成型条件や部材の変更があります。
試作のやり方ですが、まずはファーストトライ(新規金型で最初に作った樹脂ブランク)で出来上がってきたブランクをチェックします。
主にヒケやウェルド(樹脂結合が最後に行われる部分)や最終充填位置をチェクします。
強度的に不安があったりした場合は、ここでもう一回の成形トライをしてもらいます。
大事なのは、とにかく見落とさない事。
この後の部材を組んでのアクションチェックで「これで決まり」となってしまうと、もう成型条件は変更ができません。
問題がない場合は、組み付けトライへ移ります。
量産で使う「ウェイト」「ワイヤー」を組み込み、塗装工程を実際に行います。
組み付け上の不具合はないか?
部材の不具合はないか?
等です。
問題がなければ、次のフィールドテストとなります。
つづく
- 2016年10月14日
- コメント(1)
コメントを見る
fimoニュース
登録ライター
- 修羅のように
- 1 日前
- はしおさん
- お盆に釣りにいってはいけない…
- 2 日前
- papakidさん
- イワシの状況をカモメの動きで…
- 3 日前
- BlueTrainさん
- ランブルベイト:ハオリスライ…
- 5 日前
- ichi-goさん
- 天気予報は複数用いるべし
- 5 日前
- 濵田就也さん
本日のGoodGame
シーバス
-
- 下越サーフでアイザー125F置いておい…
- そそそげ
-
- BELUGA復帰戦
- ハマコー
すごい!
ルアー造りの工程
プロダクトの肝の部分の話なかなか聞けるものじゃない部分ですよね
ずすき